Even self-driving field robots affect soil functions
According to two new publications from Aarhus University, lightweight self-driving field robots, just like regular tractors, can impact the physical properties of the topsoil (0-20 cm) and increase the risk of soil compaction. The researchers provide insights into the consequences of repeated robot operations in agriculture.
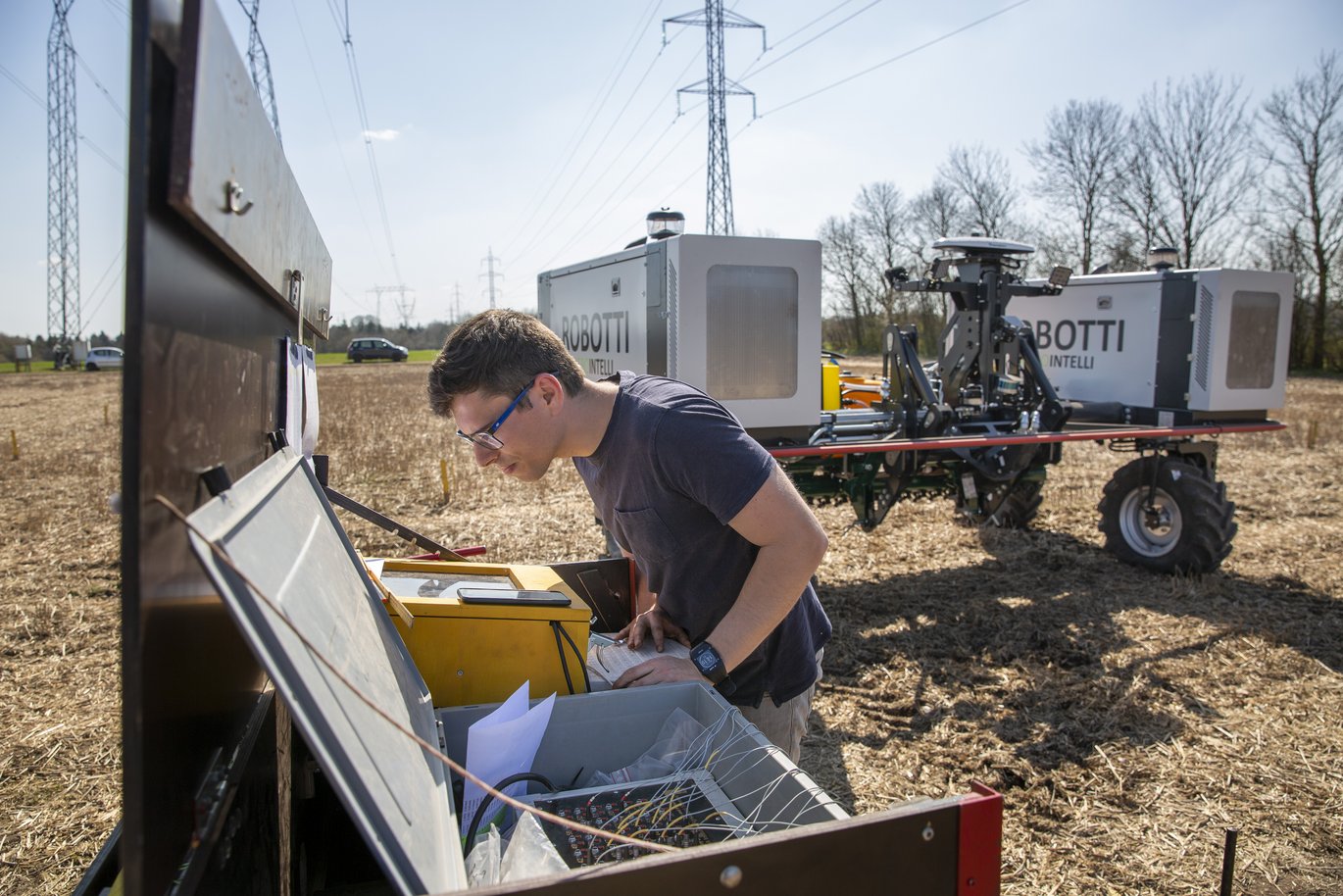
When machines drive on the soil, it gets compressed, a phenomenon known as soil compaction. Soil compaction is one of the major threats to soil quality. Compacted soil affects drainage, increases the risk of erosion, and hinders root growth. Ultimately, this can result in yield loss, increased nutrient and greenhouse gas losses, as well as flooding.
"As agricultural machinery gets bigger, soil compaction also becomes a bigger problem," says Professor Lars J. Munkholm from the Department of Agroecology at Aarhus University.
There is a constant development in agricultural machinery, and although tractors are becoming larger and heavier, the risk of soil compaction can be reduced with modern low-pressure tires and tire pressure regulation. However, it's not just tractors that have evolved technically. The technology for self-driving field robots is rapidly advancing, and robots are already operating in Danish fields. They are not as big as tractors and weigh less. The reduced weight lowers the risk of compaction in the subsoil, but does that also mean that robots can help reduce soil compaction in the topsoil?
Researchers from Aarhus University have investigated this.
Affects a larger area
"Field robots are significantly smaller than tractors. They are narrower and can thus carry less, they have a smaller capacity. This means that the area traversed increases when transitioning to robot cultivation, and the area with repeated robot operations in the field will also increase," says Professor Lars J. Munkholm.
A small field robot needs to travel back and forth several times on the field to cover the same area as a large tractor, resulting in more wheel tracks that will be used multiple times.
In a new study, with results published in two scientific publications, researchers have examined the extent to which the physical properties of the soil are affected by repeated operations of a field robot model called ROBOTTI 150D with 320/65 R16 tires. The study looked at the impacts of up to ten passes in the same wheel tracks.
"Our measurements show that the number of times the field robot operates in the field significantly affects soil compaction of the topsoil. We have measured the depth of the wheel tracks, soil penetration resistance, air permeability, and soil porosity. Although our measurements of soil compaction do not exceed critical limits, we can still clearly see that repeated operations of this type of field robot will affect the functionality of the topsoil, especially after six to ten passes in the same tracks," says Ph.D. student Alvaro Calleja Huerta from the Department of Agroecology.
Higher impact than expected
In addition, the researchers have investigated how the load from the field robot is distributed in the wheel tracks. They installed load transducers in the soil to measure the loads, their direction, and movement. They then compared the results with calculations based on the Terranimo® model.
Fact box - Terranimo®
|
According to the researchers, there is a significant increase in soil pressure with repeated operations of the field robot. The measured values turned out to deviate from the values calculates by the model. The maximum vertical loads were 32% larger than the model's predictions.
"Based on our measurements and comparisons, we found a significant increase in soil compaction with repeated passings. We could see that the values we measured in the soil differed from the values predicted by the model, and the effect turned out to be even larger. This tells us that using static loads as input in models can result in inaccurate predictions of effect under dynamic conditions. This can ultimately make it difficult to find the correct adjustment of tire pressure in the field, which can lead to further soil compaction," says Senior Researcher Mathieu Lamandé from the Department of Agroecology.
Does not exceed critical limits
Although the observed changes in the soil's physical properties do not exceed the critical limits for soil compaction, the researchers conclude that the functionality of the topsoil is negatively affected by repeated operations of a field robot. This is especially true if it operates in the same location between six to ten times.
"Field robots reduce the risk of subsoil compaction and can help reduce topsoil compaction if combined with other factors like large low-inflation tires, monitoring soil strength, using tools like Terranimo, and limiting the number of operations in the field. We need multi-season studies combining robots and traditional machinery where economic, operational, and sustainability aspects are considered to assess the real potential of lightweight robots for maintaining optimal soil quality and productivity," says Alvaro Calleja Huerta.
ITEM | CONTENT AND PURPOSE |
---|---|
Collaborators | Department of Agroecology at Aarhus University, Norwegian University of Life Sciences, and Agro Intelligence ApS. |
Funding | The study is funded by the Innovation Fund Denmark (Grant no. 9092-00007B). |
Conflict of interest | None |
Link to the scientific article | The publications "Impacts of load and repeated wheeling from a lightweight autonomous field robot on the physical properties of a loamy sand soil" and "Vertical and horizontal stresses from a lightweight autonomous field robot during repeated wheeling" are published in Soil & Tillage Research. They are written by Alvaro Calleja Huerta, Mathieu Lamandé, Ole Green and Lars J. Munkholm. |
Contact information | PhD student Alvaro Calleja Huerta, Department of Agroecology, Aarhus University. Email: a.calleja@agro.au.dk Senior Researcher Mathieu Lamandé, Department of Agroecology, Aarhus University. Tel.: 22240870 or email: mathieu.lamande@agro.au.dk |